Types of Pipes and materials used in Oil and Gas Industry
Hierarchy
From simple to most complex machines, there is always a hierarchy of importance and assistance in used materials. The quality of material determines the efficiency of the machine. For example, the knife blade (metal) is more important than its handle (insulator), but in a school desk the legs (metal) need to be more robust than top (wood).
In the Oil and gas industry hierarchy goes like-
- Pipes: From the extraction in rigs to the petrol pump nozzle going into your car tank, pipes are the most basic and integral type of equipment.
- Valves: Valves control the flow of the liquids.
- Fittings and flanges: Fittings and flanges are used to branch the pipes to multiple channels.
- Accessories: Accessories include gaskets, nuts, bolts and tools to put them in place.
(This whole writing is for pipes, there are separate contents for each of the hierarchical categories, do check all the others as well.)
Pipes
Pipes used in the oil and gas industry have a bigger diameter and more tensile strength than regular water pipes. Depending on the size of the reservoir, pressure of the flow, and conditions outside determines the selection of pipes.
Have you pondered what would happen if you use cast iron pipes in humid or hot areas? It would rust or burst after expansion due to the heat. The types of pipes mainly used here are, seamless (moulded in cylindrical shapes), ERW (electric resistance welding), and LSAW (longitudinal submerged arc welding).
Seamless Pipes
Material
Most commonly used material for making seamless pipes are:
ASTM A53, A106, A333, and API 5L (carbon steel pipes, high and low-temperature carbon steel)
ASTM A335 Grades P5 to P91 (chrome-moly alloy steel pipes, high temperature and pressure)
ASTM A312 Series 300 and 400 (stainless steel pipes)
ASTM A790/A928 (duplex and super duplex pipes, double ferritic and austenitic structure)
ERW Pipes
ERW pipes are made using steel coils: the coil is first uncoiled, then smoothed, cut and finally formed into a pipe shape by joining its two extremities electrically (high frequency A.C. current is used to produce a higher quality weld). ERW pipes are used for the same processes as seamless pipes.
But as we are advancing in the welding technologies, ERW pipes are as strong as Seamless and are cheaper than seamless.
Material
carbon steel (ASTM A53 is the most common specification)
stainless steel (ASTM A312)
LSAW Pipes
An LSAW pipe (“submerged arc welding”) is made by cutting, bending and welding steel plates. ERW and Seamless pipes don’t cross the 24″ diameter threshold or it loses its strength and purpose. At that need, LSAW becomes the leading option.
The two main types of LSAW pipes are the longitudinal (with a single or double straight seam weld, DSAW) and the spiral type (called, HSAW, SSAW or SAWL pipe). The difference between DSAW and LSAW is that DSAW pipes have a seam weld in the inside and outside of the pipe, while LSAW pipes have a single seam weld.
The integral difference between LSAW and ERW pipes is that LSAW pipes are produced using steel plates, while ERW pipes are manufactured starting from steel coils. Generally, the purpose of LSAW is not the same as the former two options. LSAW is used more in transportation of assisting fluids; like water distribution and transmission, bringing in hydrocarbons but not majorly for oil and gas.
All pipes have their strengths and weaknesses, because the intent with which each was created are different. LSAW pipes have comparatively larger diameter but have lower threshold and strength than ERW and Seamless. Hence it’s mostly used in transportation of other liquids in the extraction process. Seamless is the best option to go for, its SDR and material strength is better than ERW. Although Seamless can crack your pockets more than ERWs. With newer technologies coming up, ERWs are raising their standards to seamless pipes. Even now going for ERW is a great option.
We, at SarsanOSC, deal, stock and supply all three above-mentioned types of pipes. Ranging from 1/2” to 48” ODs in standard and line pipes. We use –
ASTM/ASME A/SA 106 Gr. B
ASTM/ASME A/SA 333 Grade 6
ASTM/ASME A/SA 53 Gr. B
API 5 L, X42, X52
ASTM/ASME A/SA 312 TP304/L, TP316/L
to make it seamless. EFW and LSAW is also a part of our catalogue.
Related News
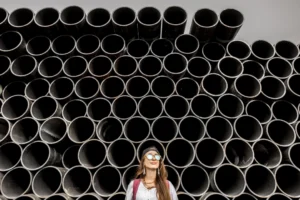
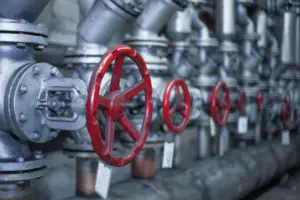

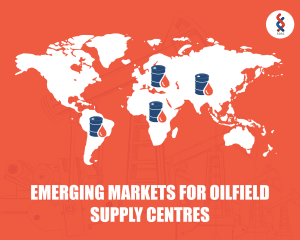
Emerging Markets for Oilfield Supply Centres
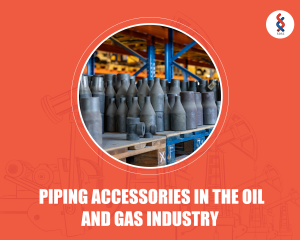
Piping Accessories in the Oil and Gas Industry
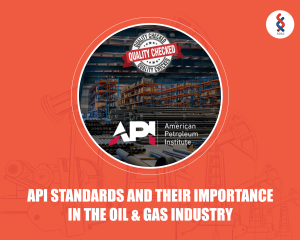